The isotropic nanotechnology breakthrough came from a grant by Oak Ridge National Laboratory. The purpose of the grant was to promote innovations through science. The results of the Frictional Behavior Test performed by Dr. Ronald Ott at Oakridge National Laboratory saw a friction reduction of 85% on treated metal. The positive results of the study confirmed the effectiveness of the treatment. Sandia Labs has also tested and verified the process and results.
The results from Oak Ridge National Laboratory and Sandia Labs were further tested in markets including racing, firearms, industrial tools, components, and many others. Positive field tests are continuing in other industries.
Major Benefits Include:
Reduces metal to metal friction by up to 85% when both pieces of the metal are treated
Treatment is permanently in the metal
Calcium molecules are fused into the molecular fabric of the metal
Heat and pressure cause the nanoparticles to elongate forming a protective shield
Operates in temperatures up to 900º
Does not alter dimensional tolerances
Saves time and operation costs
THE NANOTECHNOLOGY PROCESS
The treatment is a simple bath submersion process which covers 100% of the exposed surface. The process requires some heat, but does not exceed 200°F. It does not affect the mechanical properties, hardness, or temper the material.
The process is a treatment, not a coating, because it becomes a part of the base material, effectively eliminating any dimensional change to the part due to wear.
How do I know it was treated?
Untreated
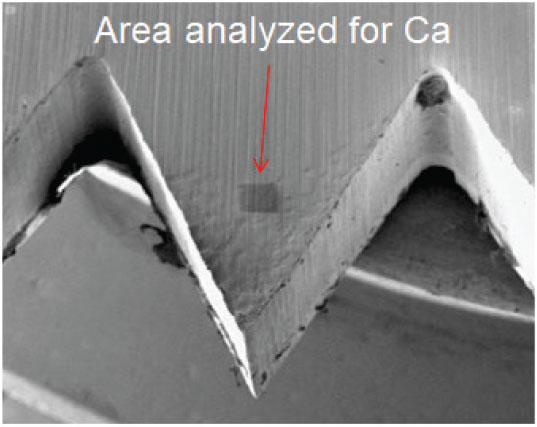
Secondary Electron Image of Untreated Saw Blade
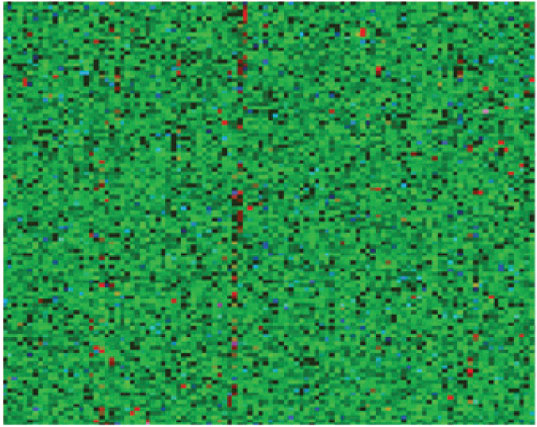
The random blue dots are from the “noisy” Ca map. (Spectral data showed noCa on this surface.)
Treated
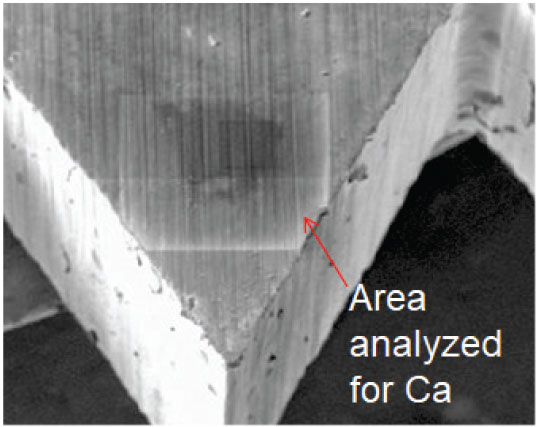
Secondary Electron Image of Treated Saw Blade
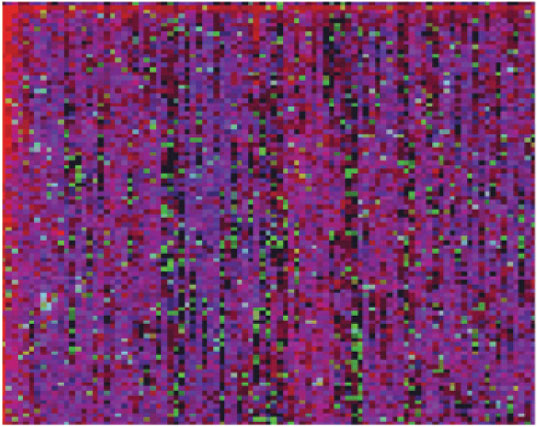
Combining the fe, C, and Ca mapts creates a magenta color due to the dominant C (red) and Ca (blue) signals. Green areas reveal where Fe is present.
“The treated bearings outperformed the untreated bearings significantly in the micro-pitting, and the treated bearings were able to achieve more than 34% more cycles to failure than untreated bearings in the scuffing tests. In my opinion, the treatment could provide a significant benefit to the performance of rolling element bearings in many applications. Based upon our test results, it looks like you have something of value to rolling element bearings. Congratulations.”
“The process has been beneficial to Gerdau by increasing bearing life and saving time and money by eliminating the need to grease bearings. We also avoid marking the finished product with dripping grease in high heat applications.”
“Our AT30 Rockmaster tool has many components that have made it a success. None are more important than the treatment that has essentially doubled the life of the bearings in the tool. Since we began exclusively using this process for the AT30 Rockmaster tool, our customers have been extremely pleased with the results.”
“Thank you for helping Mohawk with the bearing problem on our extruder motors. Normally we would install a matched set of bearings exceeding $500 on these motors and only getting a few months of life out of them. With this treatment introduced on a standard set of bearings, we have exceeded more than a year and bearing are still performing today without failure, and a greatly reduced initial cost to Mohawk.”